What you need to know about Metal Door Frames
Metal door frames (aka steel door frames, hollow metal door frames, and man door frames) have been around since the early 20th century. They appeared around the same time as metal doors and steel doors and were first promoted for their fire resistance. By the mid-20th century multiple companies had started to manufacture hollow metal doors and hollow metal frames. Today, millions of steel doors and steel frames are manufactured annually around the world.
Man door frames are commonly produced from steel, either cold rolled, galvanized, or galvannealed steel. The galvanized and galvanealed metal frames offer improved corrosion resistance over the cold rolled steel frames. Regardless of the steel type, most manufacturers apply a primer paint to the doors and frames prior to shipment to their customers. These frames are also produced from stainless steel when a high aesthetic finish is preferred.
Steel door frames are also produced from hot rolled steel. These frames are most often found in heavy industrial applications where resistance to damage from impact, for example, is desired or required.
Another material door frames and doors are produced from is aluminum. Aluminum is preferred for its appearance and corrosion resistance properties (although aluminum does corrode over time as does a steel door and metal door frame).
There are also doors and frames produced in fiberglass. These are often found in high traffic areas where high corrosion resistance and impact resistance is desired, e.g., schools.
Metal door frames have historically been available in two types, i.e., welded hollow metal and knock down configurations. The welded hollow metal frames consist of two vertical jambs and a horizontal header welded at the intersections of the jambs and header. These welded metal frames are noted for their strength and durability. They are used most often in commercial buildings for both interior and exterior building openings. These welded frames must be installed prior to the construction of the facility’s walls. As such, they can cause schedule delays if they do not arrive on site at the appropriate time. They are also subject to trade damage, i.e., damage caused by the various work trades going through the frames while the building is under construction. Trade damage can be a significant cost on a large construction project and cause delays in turning the building over to the owner.
The second type of frame, i.e., knock down, is so named because they are not welded but are assembled on the job site. In other words they are supplied in a “knocked down” condition, i.e. as separate components. One type of knock down frame is essentially a non-welded hollow metal frame. It consists of two vertical jambs and one horizontal header. These frames are installed after the walls are constructed. In that way they help to avoid schedule delays and minimize trade damage as you cannot damage a frame that is not there. While there are benefits to these frames, they do not offer the same strength or durability of the welded frames. A typical complaint is visual separation of the upper corners after just a few years.
The other style of knock down frame is most frequently known by the manufacturers brand names, i.e., Timely or Dunbarton Corporation. These companies produce similar products that are assembled on the job site. Each frame system includes a minimum of 9 pieces. One benefit of these frames is they are often supplied pre-finished and come in a wide variety of colors. While again they offer the benefit of minimizing delays and trade damage, they also do not provide the strength and durability of the welded hollow metal frame.
Millions upon millions of metal door frames have been installed since these frames became generally available. Each type has its own strengths and weaknesses.
Today, there is increasing interest in applying lean manufacturing principles to the construction work site. Lean is a discipline of driving wastes out of the processes and has the goal of providing the customer with the best value at the best cost. The best customer value would be a welded frame that could be installed after the walls are built and minimizes the labor effort and cost in doing so.
The Qwikinstall frame system accomplishes both of these goals. It is a two-piece interlocking welded hollow metal frame that installs after the walls are complete. It installs with 1 person, in 6 steps, in 6 minutes. No other welded frame installs faster than Qwikinstall and no other frame combines the strength and durability of welded frame with the benefits of installation after the walls are complete.
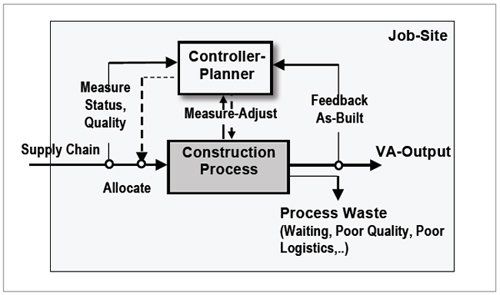